Lean Process And Six Sigma
You’ll develop the cultural awareness and critical thinking skills you need to analyze and produce a broad range of discourse in a full spectrum of careers — and to make a difference in whatever you do.
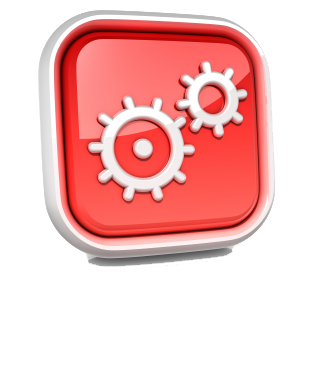
- 12 Moduls / 3 Weeks
- Intakes: Asynchronous, Apply to Enroll
Overview
What is “Sigma”? The word is a statistical term that measures how far a given process deviates from perfection. Sigma is a way to measure quality and performance. The central idea behind Six Sigma is that if you can measure how many “defects” you have in a process, you can systematically figure out how to eliminate them and get as close to “zero defects” as possible. This course will give participants an overview of the Six Sigma methodology, and some of the tools required to deploy Six Sigma in their own organizations.
Program Learning Outcomes
This course is designed to help you in the following ways:
- Develop a 360 degree view of Six Sigma and how it can be implemented in any organization.
- Identify the fundamentals of lean manufacturing, lean enterprise, and lean principles.
- Describe the key dimensions of quality – product features and freedom from deficiencies
- Develop attributes and value according to the Kano Model
- Understand how products and services that have the right features and are free from deficiencies can promote customer satisfaction and attract and retain new customers.
- Describe what is required to regulate a process
- Give examples of how poor quality affects operating expenses in the areas of appraisal, inspection costs, internal failure costs, and external failure costs
- Using basic techniques such as DMAIC and how to identify Six Sigma Projects
- Use specific criteria to evaluate a project
- Discover root causes of a problem
- Design and install new controls to hold the gains and to prevent the problem from returning.
Course Modules
Module Name | ||
---|---|---|
Module One: Getting Started | ||
Module Two: Understanding Lean | ||
Module Three: Liker’s Toyota Way | ||
Module Four: The TPS House | ||
Module Five: The Five Principles of Lean Business | ||
Module Six: The First Improvement Concept (Value) | ||
Module Seven: The Second Improvement Concept (Waste) | ||
Module Eight: The Third Improvement Concept (Variation) | ||
Module Nine: The Fourth Improvement Concept (Complexity) | ||
Module Ten: The Fifth Improvement Concept (Continuous Improvement) | ||
Module Eleven: The Improvement Toolkit | ||
Module Twelve: Wrapping Up | ||
. |
Do you have more questions?
Contact us
1050 West Lakes Drive, # 225
West Covina, CA 91790
How to Apply?
- You Apply
Tell us a little about yourself and we’ll help with the rest. Our convenient online application tool only takes 10 minutes to complete.
- We Connect
After you submit your application, an admissions representative will contact you and will help you to complete the process.
- You Get Ready
Once you’ve completed your application and connected with an admissions representative, you’re ready to create your schedule.